The Basics
What is sheet metal fabrication?
Sheet metal fabrication is the process of bending, cutting, and/or punching sheet metal to form into a functional part. The basic process can be simplified into three main steps. First, a 3D model of the design is created using CAD software. Then the CAD file is converted into machine code and the machine is set up. Finally, the machine precisely forms the sheet metal into the desired shape using one or a combination of the processes mentioned above.
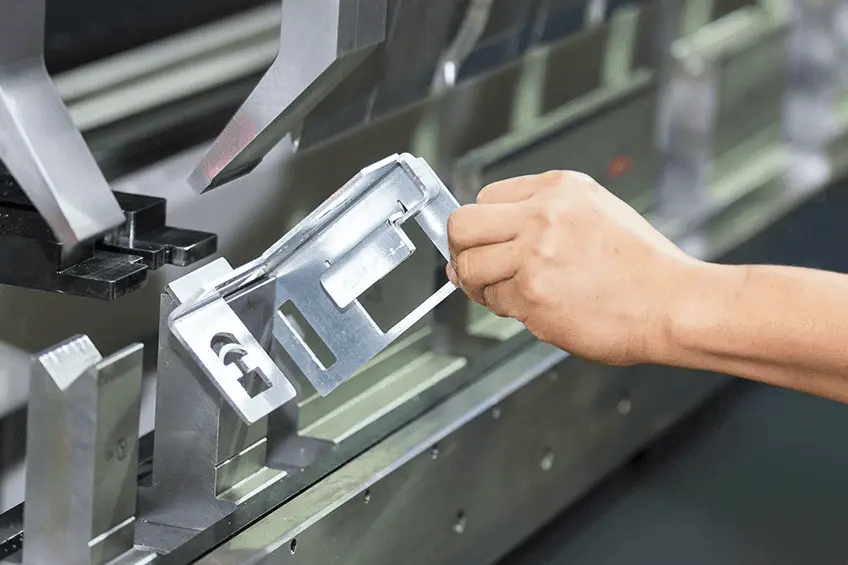
Parts are manufactured from a single piece of sheet metal so designs should have a uniform thickness to them. Sheet metal comes in a range of thicknesses from 0.5 mm - 6 mm, anything thicker than this is considered metal plate, thicknesses up to 20 mm can be manufactured. Parts manufactured using sheet metal fabrication are known for their durability and can scale from one-off prototypes to high-volume production.
{{cta-banner}}
What are the different types of sheet metal fabrication?
Laser Cutting
One of the key methods for cutting sheet metal is using a laser cutter. Laser cutting uses a high energy beam that is intensified with a lens or mirror to burn/vaporise the material to form a cut. It is a very quick and precise method for cutting sheet metal and has a reduced chance of warping due to the small heat-affected zone. C02 and fibre lasers are most commonly used and can cut material up to 10 mm thick.
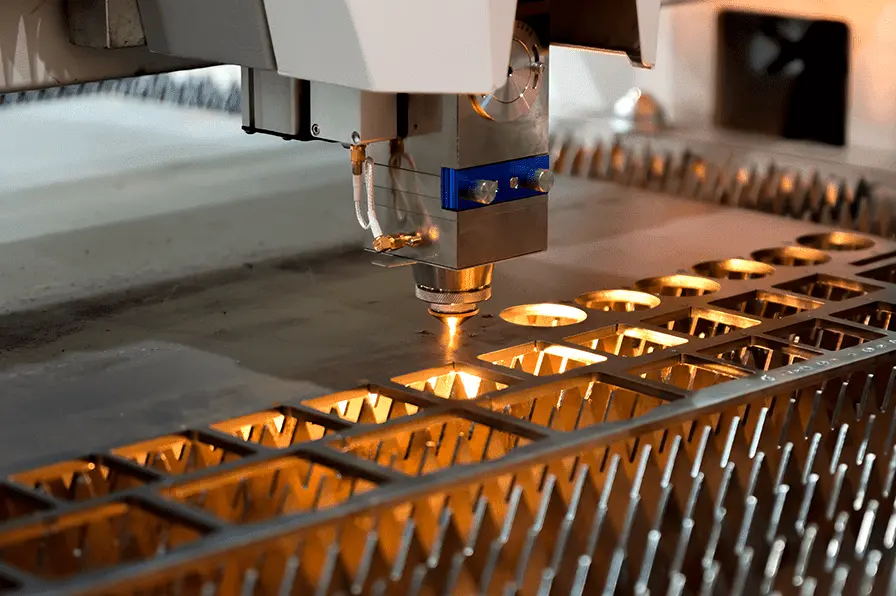
Water Jet Cutting
Another sheet metal cutting method is water jet cutting. Water jet cutting uses an extremely high-pressure jet of water (which can also be mixed with an abrasive substance) to form the cut in the material. It is a preferred fabrication method over laser cutting when cutting materials with a low melting point such as plastics and aluminium to prevent unwanted deformation.
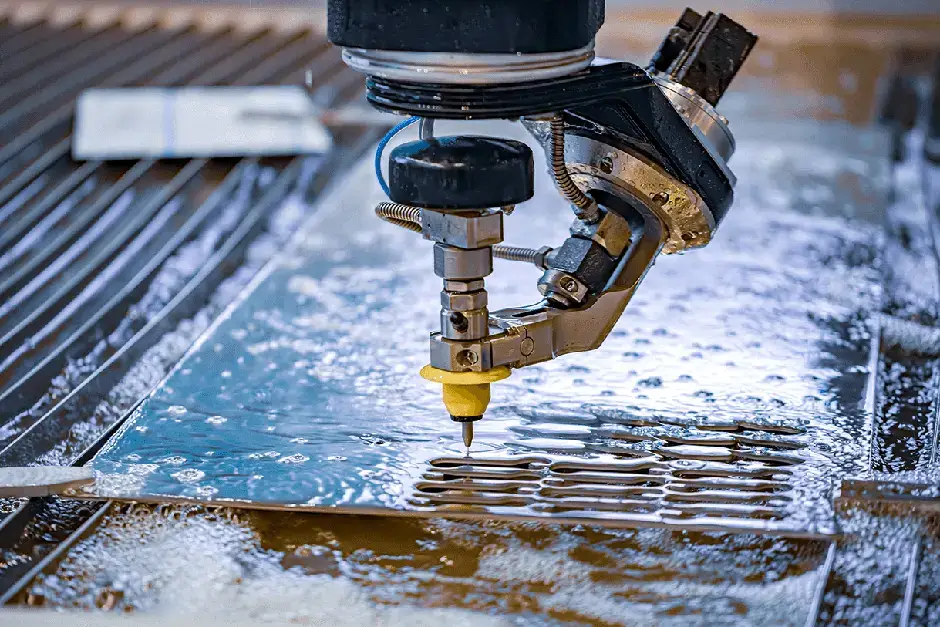
Plasma Cutting
The third and most powerful sheet metal cutting method is plasma cutting. Plasma cutting works by creating an electrical channel of extremely hot, electrically ionised gas (plasma) which melts the material to form the cut. It is an effective method for cutting material over 10 mm thick, however, the precision of the cut is not to the same level as laser or water jet cutting.
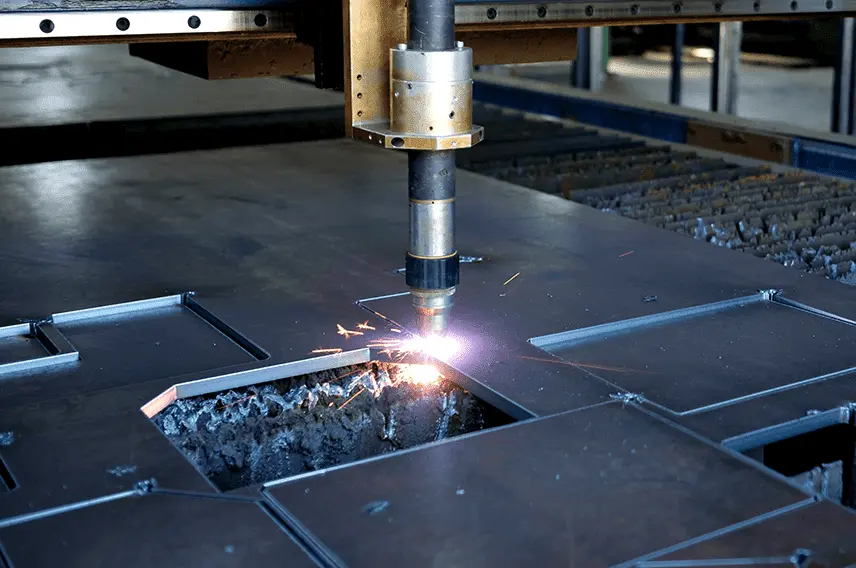
Guillotining
Sheet metal guillotines are an effective method for creating clean, accurate cuts in sheet metal. The sheet is fed between two blades which are then compressed together at a high force to deform the sheet until it eventually produces the cut. Guillotining is a quick and inexpensive method for producing high-quality cuts, although it can leave the metal with a slightly deformed edge.
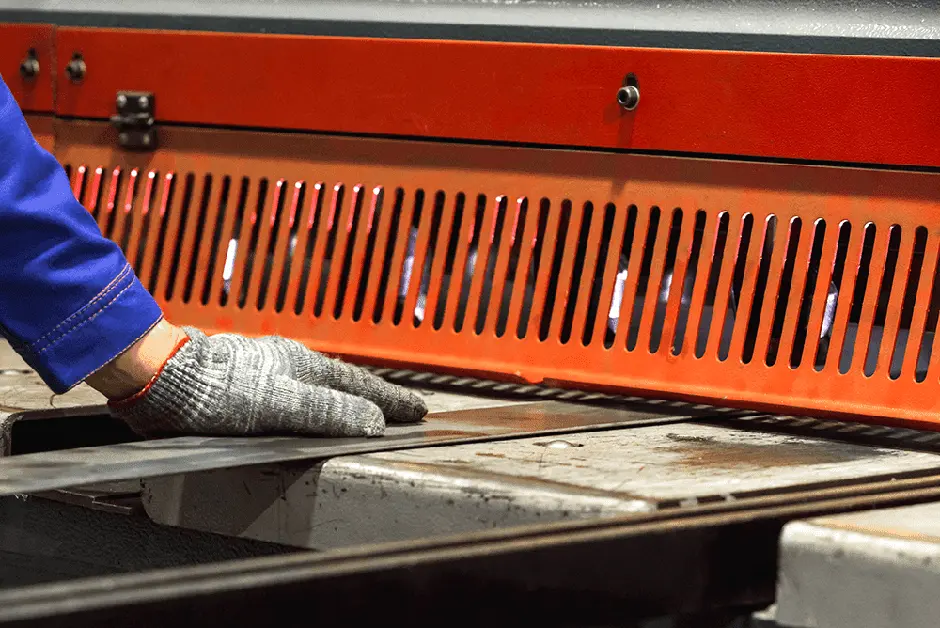
Punching
Sheet metal punching uses a similar cutting mechanism to guillotining however, it uses a shaped metal tool (known as a die) to make the cut. The die is forced into the sheet metal at a high speed to perforate the sheet. Dies of standard shapes (circle, square, rectangle) are commonly used however, custom tooling can be made for punching more complex shapes. This method is better suited for high volume production due to the cost of manufacturing the die.
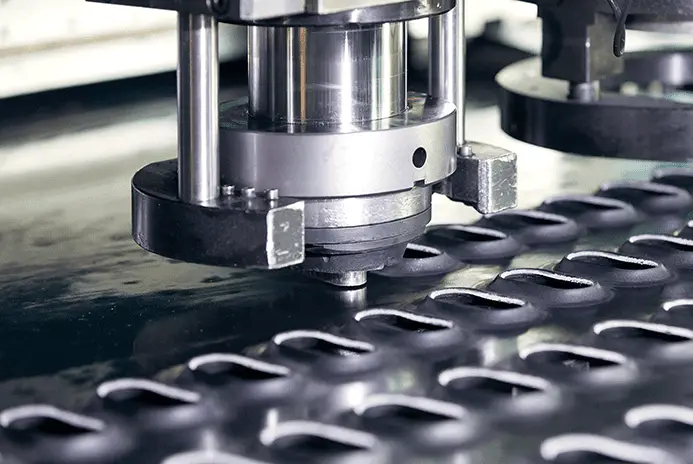
Bending
Bending is a fundamental manufacturing process to form sheet metal into functional parts. Sheet metal is bent using a machine known as a press brake comprised of an upper tool (punch) and a lower tool (V-die). Material is placed between the tools and the punch presses down into the V-die to form the bend. The bend angle is determined by the depth the punch is pressed downwards into the V-die.
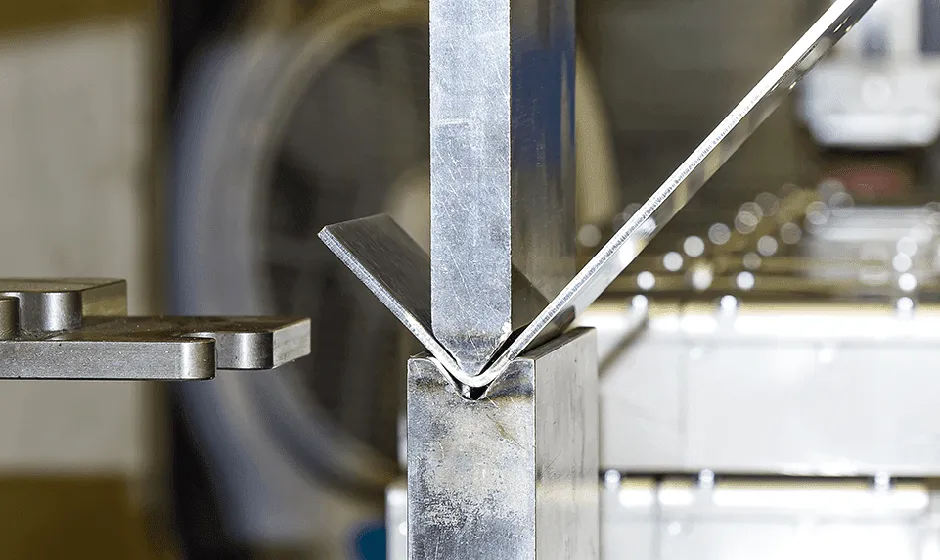
Assembling
Cutting and bending are two ways of forming sheet metal, assembly is the third way. Assembling sheet metal components can be achieved using mechanical fasteners such as bolts, screws and rivets. Or they can be joined using the process of welding, where two or more parts are fused together using intense heat and then allowed to cool to form a join.
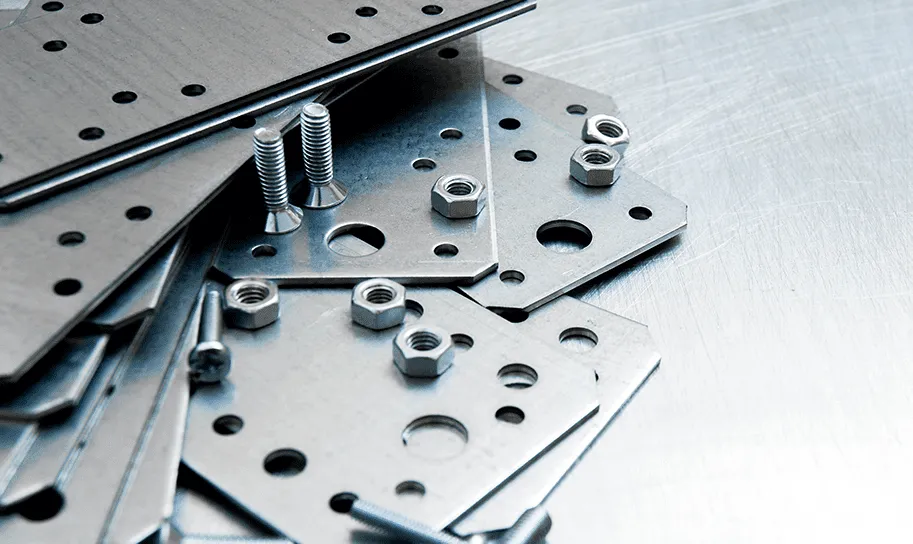
Advantages of CNC Sheet Metal Fabrication
✅ Cost-effective
Sheet metal fabrication is a fast and cost-effective solution for manufacturing a one-off prototype design up to a high volume production run of thousands of parts. With the ability to automate a lot of the process the manufacturing process can efficiently scale to very high volume production.
✅ Material Selection
A broad range of materials can be used for sheet metal fabrication. Sheet metal can be made from a variety of materials that each have their own individual characteristics and offer unique characteristics.
✅ Lightweight
A lot of materials that are known for their durability come with a weight penalty. Metal sheets are lightweight so sheet metal fabrication can offer the durability of a material with the combination of being lightweight and highly portable.
Disadvantages of CNC Sheet Metal Fabrication
❌ Complex Designs
Sheet metal fabrication is a very flexible manufacturing process however, some materials are not malleable enough to be formed into highly complicated shapes or designs. So there are some design limitations on what materials and thickness of material can be used when designing complex components.
❌ Fixed Uniform Thickness
Parts are formed from a single piece of sheet metal which restricts the design to a uniform thickness throughout.
Sheet Metal Design Guidelines
Bending
As mentioned earlier sheet metal is bent using a machine known as a press brake comprised of an upper tool (punch) and a lower tool (V-die). Material is placed between the tools and the punch presses down into the V-die to form the bend.
Bend relief
When a bend is made close to the edge of the sheet it runs the risk of tearing. To eliminate this a relief should be added to help control the sheet metal material behaviour and prevent unwanted deformation during bending operations. The relief cut should be rectangular with a depth more than the bend radius and width greater than the material thickness. A corner relief notch should be added if two bends extend all the way to the edge of the part. Various cutouts shapes can be used to create the relief but the depth should be no deeper than the material thickness plus bend radius.
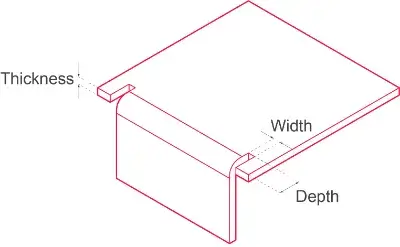
Bend height
To ensure a high-quality bend the height of the bend should be at least 2x the thickness of the material plus the bend radius. If the height is too small the sheet metal will not deform correctly when bending.
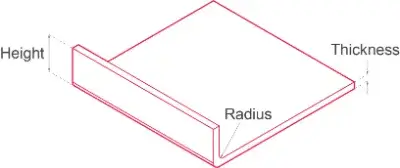
Bending next to holes
If a hole is placed too close to a bend line it can be pulled out of shape by the action of the bend that is too near to it. Sometimes this is not an issue if it is simply a clearance hole for a screw or bolt however, for holes that are to be threaded this will cause tapping issues.
There are two formulas that can be used to ensure the holes in your design do not fall into the bending deformation zone when close to a bend. If the hole has a diameter less than 25 mm, the hole should be placed at a distance 2x the thickness of the material plus the bend radius from the outside edge of the bend (d = 2t + r). If the hole diameter is greater than 25 mm, the hole should be placed at a distance 2.5x the thickness of the material plus the bend radius from the outside edge of the bend (d = 2.5t + r). If the holes need to be placed close to a bend they should be drilled out after the bending operation. This will increase part cost due to the additional machining time.
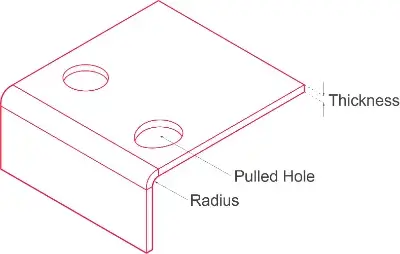
Laser cutting
There are a few things to be aware of when using laser cutting to process your parts. First, the high-intensity laser creates extreme heat in the part in order to create the cut. This creates a heat-affected zone (HAZ) along the edge of the cut. For most parts, this change in the microstructure is not an issue but for critical parts, this should be considered as the HAZ causes a reduction in material strength.
The second thing to consider is that the cut line will have a taper to some degree due to the shape of the laser. The laser cannot be focused perfectly straight through the focusing lens and as a result, the laser creates an hourglass-shaped cut. This is only noticeable on parts thicker than 1.5 mm so only needs to be considered when working with thicker sheets.
The third thing to consider is the laser burns away a portion of the material when it cuts through. This is known as laser kerf and can range from 0.05 mm - 1 mm depending on the material type and other conditional factors. Most modern CNC machines automatically adjust to take into account this offset to ensure the final dimension of the part is correct.
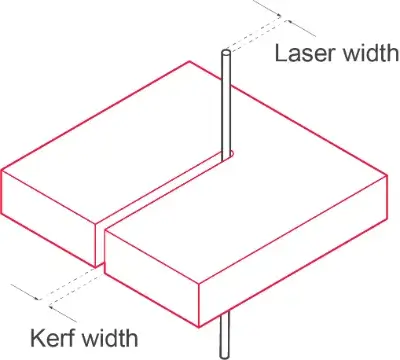
Curls
Curling sheet metal is the process of forming the edge of the sheet into a hollow ring. This method is commonly used to remove sharp edges from the workpiece so that is safe to handle.
When adding curls to your design, the outer edge radius of the curl must be greater or equal to 2x the material thickness. If you need to add holes near to a curl feature in your sheet metal, ensure they are positioned at a distance greater than the curl radius plus the material thickness. A bend feature should be located no less than the distance of the curl radius plus 5x the material thickness from a curl feature.
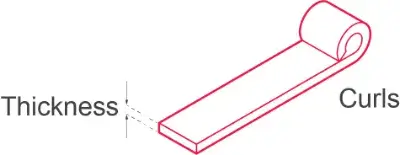
Countersink holes
Countersink holes are conical shaped holes and are added to parts to allow the head of a countersunk bolt/screw to sit flush with the surface of the sheet metal.
Countersinks should be a distance of 8x the material thickness from another countersink, 4x the material thickness from the material edge and 3x the material thickness from a bend.

Hems and seams
Hemming and seaming are two similar fabrication methods where the edge of the sheet is rolled/folded over on itself. Hemming is the process where the edge is folded back on itself to sit flush, while a seam joins the edges of the two materials. Hems are commonly used to remove sharp edges so they are safe to handle, improve the appearance and reinforce the edges. Seams are used to join two pieces of sheet metal together. For example, the join between the lid and the can on a baked bean tin is a seam.
The inside diameter of an open hem should be no less than the thickness of the material, and the folded sheet should return back against the sheet at least 4x the thickness of the material. For a flattened hem, the folded sheet should return at least 8x the thickness of the material. A teardrop hem is used when the material does not have the ductility required to form a flattened hem. The same design rules apply to a teardrop hem as they do to an open hem.
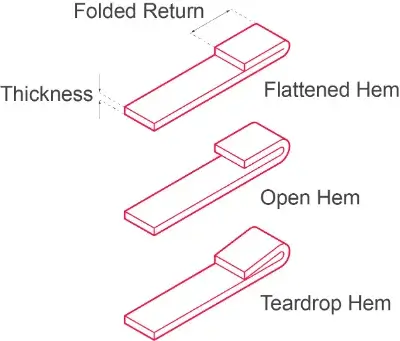
Holes and slots
When adding holes in sheet metal it is recommended to keep the diameter of the hole larger than the thickness of the sheet metal so punching equipment can be used. If a smaller hole is required punching cannot be used at the tool may break so a laser cutter needs to be used. Holes can tear if they are placed too close to a bend.
The minimum distance a hole should be from a bend is, 2x the material thickness plus the bend radius. Slots are even more prone to deforming so they should be placed at a distance of 4x the material thickness plus the bend radius from the bend. It is also important to consider how close a hole or slot can be placed to the edge of the material to avoid tearing. It is advised to place holes and slots at least 2x the material thickness from the edge. Ideally, the distance between holes should be kept at a distance of 5x the thickness of the material.
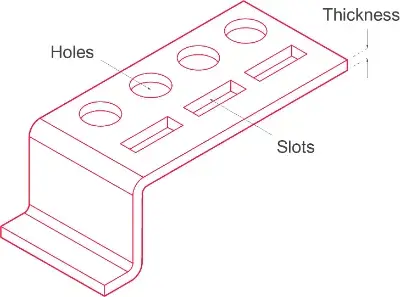
Notches and tabs
Notches are added to sheet metal by either a shearing or punching process. Usually, this method is a precursor to a forming process such as bending but they are also sometimes the sole purpose.
The minimum width of a notch should be at least the material thickness and the depth no greater than 5x the width. For bends, notches should have a width of 3x the material thickness plus the bend radius and a depth no greater than 5x the width. The width of tabs should be at least 2x the material thickness or no lower than 3 mm.
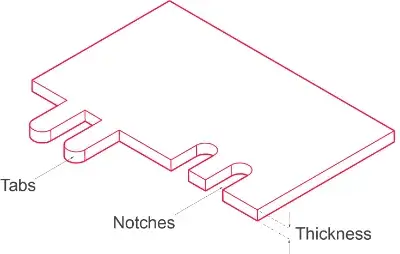
Fillets
Much like curling, fillets can be added to sheet metal to remove sharp edges, making parts safer and easier to handle. It is recommended to add a fillet with a radius equal to or greater than 0.5x the material thickness.
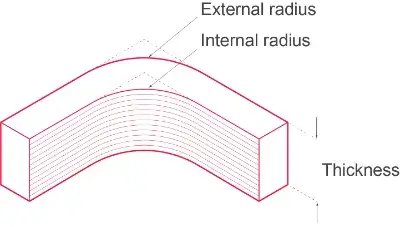
Wall thickness
It is important that parts maintain a uniform thickness throughout. Get It Made has the capabilities to manufacture sheet metal from 0.5 mm - 20 mm.
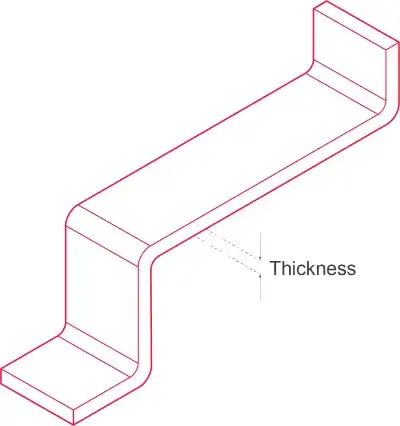
Sheet Metal Materials
A broad range of metals can be used for sheet metal fabrication and the selection should depend on the mechanical properties, thickness and desired form. The most common metals will be outlined below with their unique properties and benefits.
Hot Rolled Steel (HRS)
Hot rolled steel is steel that has been roll-pressed at very high temperatures, over 900°C, which is above the re-crystallisation temperature. The result is a steel that is much easier to form and therefore easier to work with but it is harder to keep to tight tolerances.
✅ Good formability making it suitable for a variety of shapes and forms
✅ Suitable for high volume productions
✅ Lower cost than cold rolled steel
❌ Lower achievable tolerances compared to cold rolled steel
❌ Rougher surface compared to cold rolled steel
Cold Rolled Steel (CRS)
Cold rolled steel goes through the same high temperature rolling process as HRS however, an additional room temperature rolling process is performed on the steel. The result is a steel with closer tolerances and an increase in material strength by up to 20%.
✅ Increased strength and hardness compared to HRS
✅ Tighter tolerances make true edges and square corners achievable
✅ Less spring back when forming
❌ Increased cost compared to HRS
❌ Requires additional finishing to prevent corrosion
Aluminium
Aluminium is easily alloyed with additional materials such as copper, magnesium and silicon meaning it comes in lots of different grades making it suitable for a variety of applications. Al1060 is pure aluminium with very high electrical conductivity, formability and corrosion resistance but comes at the cost of lower mechanical strength. Al5052 has the highest mechanical strength out of the non-heat-treated alloys combined with great fatigue resistance. However, the main advantage of this alloy is its ability to be formed into complex shapes.
✅ Corrosion resistant
✅ Weighs ~1/3 of other materials like steel
✅ Great formability, workability and weldability.
❌ Increased cost over steel
❌ Lower mechanical strength compared to steel
Stainless Steel
There is a range of stainless steels grades that can be used for sheet metal fabrication, all of them having a chromium content of over 10.5% making them corrosion resistant. The 300 series sheets of steel are the most commonly used as they do not require heat during the fabrication process. SS304 is ~25% cheaper than SS316 but doesn't have as good mechanical strength or resistance to corrosion in saltwater.
✅ Presence of chromium creates corrosion resistance
✅ Suitable for a wide variety of additional manufacturing processes
✅ Excellent combination of strength and hardness
❌ More expensive than aluminium and steel
❌ Corrosion can occur at thick weld points
Cold Galvanised Steel
Cold galvanised steel is steel that has had a protective zinc coating applied to its surface by brushes, sprayers or electro galvanising. The paint includes binders that cause it to mechanically bond to the steel.
✅ Provides protection against corrosive environments
✅ Cost effective way to protect steel
✅ Low maintenance and increases the life expectancy of parts
❌ Extra cleaning step required before coating
❌ Doesn't offer as good protection as hot galvanised steel
Cost Reduction Tips
This section will outline some simple adjustments you can make to your designs to help reduce the overall part cost. There are three main areas that will significantly affect the cost of your part:
- Design - Complex parts result in increased manufacturing time.
- Material - The cost of the bulk material and how easily it can be machined.
- Quantity - Cost per unit reduces with an increase in quantity due to fixed setup costs.
Design
Use simple bends
As a general rule of thumb, the more complicated your part is the more expensive it will be to manufacture. Therefore, when designing your parts try to keep the bends as simple as possible. Small bends relative to the material thickness are often inaccurate and difficult/expensive to produce.
Only apply tight tolerances to critical components
To manufacture holes, walls and threads to tight tolerances is an expensive process as it increases the overall manufacturing time for each part. Post-machining inspection using a micrometre or CMM tool is also required, further adding to the cost. It is therefore advised to only add tolerance call-outs to critical features in your design.
Design to a standard sheet gauge
Ensure your part is designed around a standard sheet metal gauge to prevent the need for additional machining. Thicker sheets may restrict your achievable design capabilities, so ensure the common gauge you select is suitable for all your bends and design features.
Keep the bend line consistent
When you have multiple flanges along the same edge it is advised to bend them all along the same bend line. If each flange is bent along a separate bend line the machine technician will have to reposition the part multiple times, increasing machining time and cost.
Use standard holes
Standard holes sizes can be drilled quickly and accurately with drill bits. However, if you require a non-standardised hole CNC machining will need to be used, increasing the cost. It is also important to keep holes a suitable distance away from the edge of the part to avoid creating a problematic thin wall feature.
Material
Two factors affect the cost of certain materials for sheet metal fabrication, the raw material cost and the machinability. Raw material costs do fluctuate over time however we keep our material prices consistent so part costs remain fixed for repeated orders. Machinability refers to how easily the material can be machined. The better the machinability of material the quicker the machining time, resulting in reduced cost. Yet the main cost of using a certain material is the bulk material price.
It is advised to select the lowest cost material that has the properties which meet your design requirements. If you are unsure about what material to select, submit a quote with us for a range of different materials to give you an idea of the price range.
Quantity
Without any design changes, the cost of your part can be reduced significantly by just increasing the order size. Our engineers have to perform the part setup, programming and tool choice which is a fixed cost. By manufacturing multiple parts at the same time the fixed cost can be shared, making each individual part more economical.
Getting Your Part Made
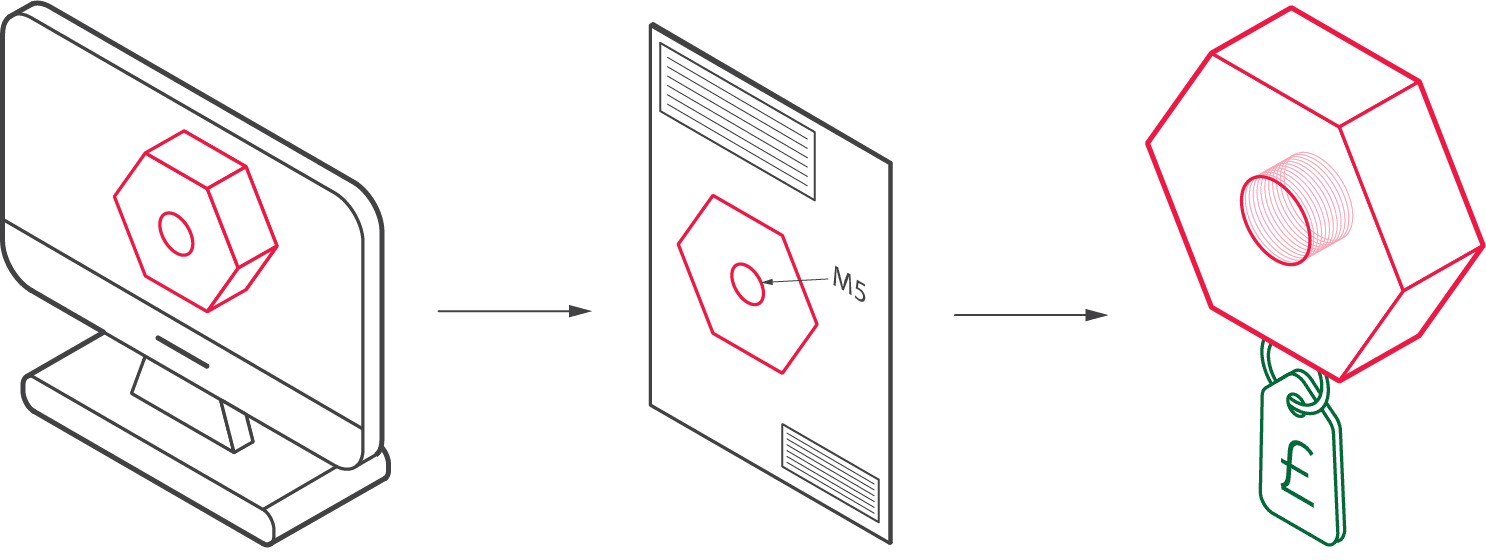
1) Design and export your CAD file
Use the Sheet Metal Design Guidelines to help design your parts ready for machining. Then please export your 3D CAD files to STEP, IGS or PARASOLID format. Unfortunately, we can only accept STL files for 3D printing projects. We cannot accept OBJ files as they do not correct geometric data for manufacturing.
2) Create an engineering drawing
We highly recommend sending supporting PDF engineering drawings for each part. This is required when a part has: thread holes, critical dimensions, tolerances, specific finishing requirements. In some circumstances such as highlighting a threaded hole, we can accept an annotated screenshot. To understand learn how to specify threads, see our threads terminology page, and our metric thread chart.
3) Get a Quote in 24 hours
Request a free quote today and one of our engineers will personally review your project within 24 hours. They will then help fine-tune your project to make sure you get the best possible price and lead time for your sheet metal parts!